When choosing between petroleum-based and synthetic lubricants, you’ll find that synthetics offer significant advantages despite their higher cost. While conventional oils need changing every 3,000-5,000 miles, synthetics can last 7,500-15,000 miles and provide better protection across temperature extremes. You’ll benefit from improved fuel efficiency, reduced maintenance, and less environmental impact with synthetics. Understanding these key differences will help you make an informed decision for your specific needs.
The Evolution of Lubricant Technology
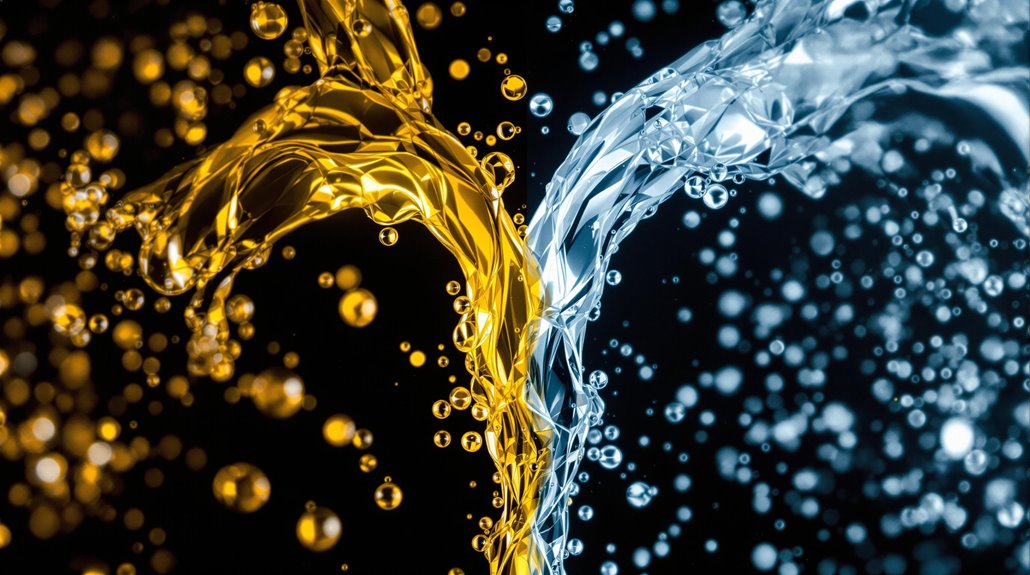
While early civilizations relied on simple animal fats and vegetable oils for lubrication, the discovery of petroleum in the mid-1800s revolutionized the lubricant industry.
You’ll find that historical advancements in refining techniques made it possible to create more effective petroleum-based oils, which quickly became the standard for industrial machinery and early automobiles.
As you explore technological innovations in lubricant development, you’ll notice how the 1940s marked a significant turning point with the introduction of synthetic oils.
These lab-created lubricants offered superior performance in extreme temperatures and harsh conditions.
Today’s synthetic oils are the result of decades of research, combining advanced molecular engineering with specialized additives to provide better engine protection, longer service life, and improved fuel efficiency compared to their conventional counterparts.
Understanding Base Oil Classifications
When you look at modern lubricants, you’ll find they’re classified into five distinct base oil groups based on their molecular structure and manufacturing process.
These classification systems help you understand the quality and performance characteristics of different base oil types you might encounter.
Groups I through III are refined from petroleum crude oil, with each group representing higher levels of processing and purity.
Group IV consists entirely of synthetic oils called polyalphaolefins (PAOs), while Group V includes all other base oils that don’t fit in the previous categories.
You’ll notice that as you move up through the groups, the oils generally become more stable, perform better in extreme temperatures, and last longer.
This standardized grouping makes it easier to compare and select the right lubricant for your specific needs.
Chemical Composition and Properties
The molecular makeup of petroleum-based and synthetic lubricants shapes their distinct performance characteristics. You’ll find that petroleum-based oils have varied molecular structures due to their natural origins, while synthetic oils feature uniform, engineered molecules that provide more consistent performance.
This fundamental difference affects how each type interacts with additives and performs under stress.
When you compare their properties, you’ll notice that synthetic lubricants offer better stability at extreme temperatures, stronger molecular bonds, and more predictable additive interactions.
Their engineered molecular structure resists oxidation and maintains viscosity more effectively than petroleum-based oils.
While conventional oils can still perform well in many applications, their irregular molecular composition means they’re more susceptible to breakdown and may require more frequent changes to maintain peak performance.
Performance Characteristics Compared
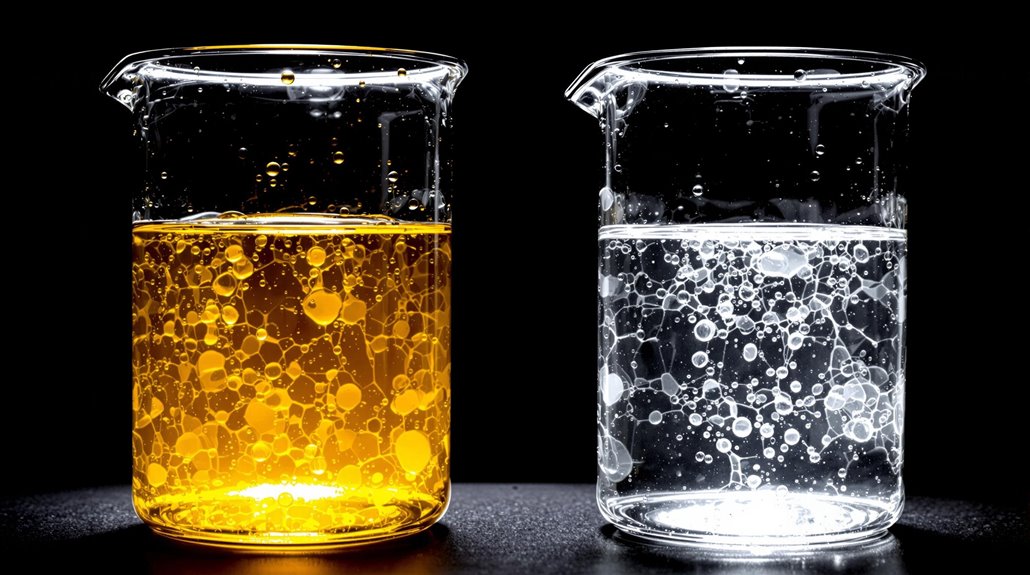
Both types of lubricants display distinct performance characteristics that you’ll notice during real-world applications.
When comparing performance metrics, synthetic lubricants consistently outperform petroleum-based options in key areas like thermal stability, oxidation resistance, and cold-weather flow.
You’ll find that synthetic lubricants offer superior lubrication efficiencies, maintaining their viscosity across a broader temperature range. They’ll protect your equipment better in extreme conditions, whether it’s scorching heat or freezing cold.
While petroleum-based lubricants are adequate for basic applications, they break down faster and require more frequent changes.
Here’s what you can expect:
- Synthetic: longer service life, better wear protection, improved fuel economy
- Petroleum-based: lower initial cost, suitable for moderate conditions, traditional reliability
Consider your specific needs and operating conditions when choosing between these options.
Temperature Stability and Operating Range
Understanding temperature stability reveals one of the most significant differences between synthetic and petroleum-based lubricants in real-world applications. You’ll notice that synthetics offer superior performance across wider temperature ranges and maintain their thermal stability in extreme conditions.
Temperature Characteristics | Synthetic | Petroleum-Based |
---|---|---|
Cold Weather Performance | -50°F to 0°F | 0°F to 32°F |
Operating Range | -40°F to 400°F | 10°F to 250°F |
Thermal Breakdown Point | Above 400°F | Around 250-300°F |
When you’re operating equipment in challenging environments, this difference becomes essential. Synthetic lubricants won’t thicken as much in cold weather or break down as quickly in high-heat situations, giving you more reliable protection and longer service intervals. They’ll maintain their viscosity better across temperature extremes, which means better engine protection and fewer cold-start issues.
Cost-Benefit Analysis and ROI
While synthetic lubricants demonstrate superior performance characteristics, many equipment operators wonder if they’re worth the higher upfront cost.
When you conduct a thorough cost analysis, you’ll find that synthetics often provide better investment returns over time, despite their premium price tag.
- You’ll typically spend 2-4 times more on synthetic oil initially, but it lasts 3-5 times longer than conventional oil.
- Your maintenance intervals can be extended greatly, reducing labor and downtime costs.
- You’ll see improved fuel efficiency of 2-3% on average, leading to substantial savings in fuel costs.
- Equipment life can be extended by 20-30% due to better protection, postponing major repairs and replacement costs.
Environmental Impact and Sustainability
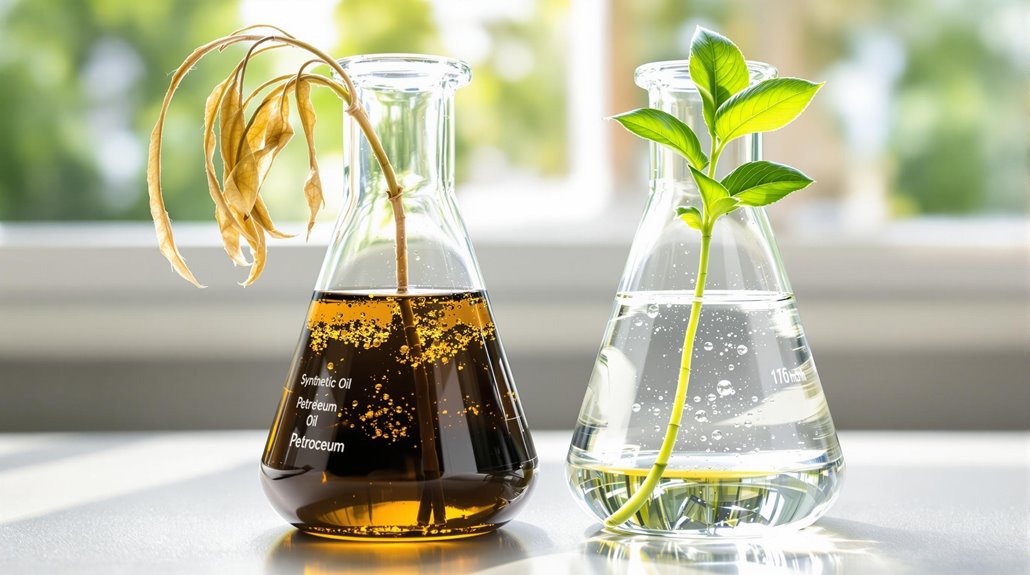
Because environmental concerns are increasingly shaping industrial decisions, the choice between petroleum and synthetic lubricants has significant ecological implications. You’ll find that synthetic lubricants align better with modern sustainability practices and environmental regulations, offering longer service life and reduced waste generation.
Environmental Factor | Petroleum-Based | Synthetic |
---|---|---|
Biodegradability | Low | Moderate to High |
Waste Generation | Higher | Lower |
Carbon Footprint | Larger | Smaller |
Resource Consumption | More frequent changes needed | Extended service intervals |
When you’re considering your facility’s environmental impact, remember that synthetics typically require fewer oil changes and produce less waste oil. They’re also more stable at extreme temperatures, which means you’ll use less energy maintaining ideal operating conditions. This improved efficiency directly contributes to reduced environmental impact and better compliance with current regulations.
Industry-Specific Applications
Since different industries face unique operating conditions and performance demands, the choice between petroleum-based and synthetic lubricants varies considerably across sectors.
You’ll need to evaluate specific requirements when selecting the right lubricant for your application, as each industry has its own set of challenges and performance standards.
- Automotive applications and heavy machinery often require synthetic oils for better engine protection and longer drain intervals, especially in extreme temperatures.
- Industrial equipment and power generation systems typically use specialized synthetic blends for enhanced equipment longevity and reduced maintenance.
- Aerospace machinery and electronic devices demand ultra-pure synthetic lubricants with exceptional stability and low volatility.
- Food processing and chemical manufacturing rely on food-grade synthetic lubricants that meet strict safety and contamination prevention standards.
Maintenance Considerations and Change Intervals
Although both petroleum-based and synthetic lubricants require regular maintenance, they differ markedly in their change intervals and upkeep requirements.
You’ll need to follow stricter maintenance schedules with petroleum-based oils, typically changing them every 3,000-5,000 miles in vehicles or every 3-6 months in machinery.
Synthetic lubricants, however, can last considerably longer. Your synthetic lubricant lifespan can extend to 7,500-15,000 miles in vehicles or 6-12 months in industrial equipment, depending on operating conditions.
When maintaining either type, you should:
- Monitor oil color and consistency
- Check for metal particles or contamination
- Document change dates and mileage
- Test oil quality regularly
- Store unused lubricants properly
Remember to adjust these intervals based on your specific application, environmental conditions, and manufacturer recommendations.
Future Trends in Lubricant Development
While lubricant technology has evolved considerably over the past decades, you’ll find even more exciting innovations on the horizon.
The industry’s focus on sustainability and performance is driving rapid changes in how lubricants are developed and manufactured, with consumer education playing a crucial role in adoption.
- You’ll see more biodegradable options derived from renewable sources, as market demands shift toward environmentally friendly alternatives.
- Innovative additives will emerge to enhance lubricant performance while meeting stricter regulatory changes.
- Alternative technologies, including smart lubricants that can self-monitor and report their condition, will become more common.
- Advanced synthetic formulations will offer extended service life and improved performance enhancements, particularly in extreme conditions and specialized applications.
Conclusion
Just as you’d choose between traditional and modern building materials, your lubricant choice shapes your equipment’s future. You’ll find that synthetic oils generally offer superior performance and longevity compared to their petroleum-based counterparts, but they’re not always necessary for every application. Consider your specific needs, operating conditions, and budget when making your selection. With proper research and maintenance, you’ll keep your machinery running smoothly for years to come.